Changing How to Build with Hal Macomber Part 2
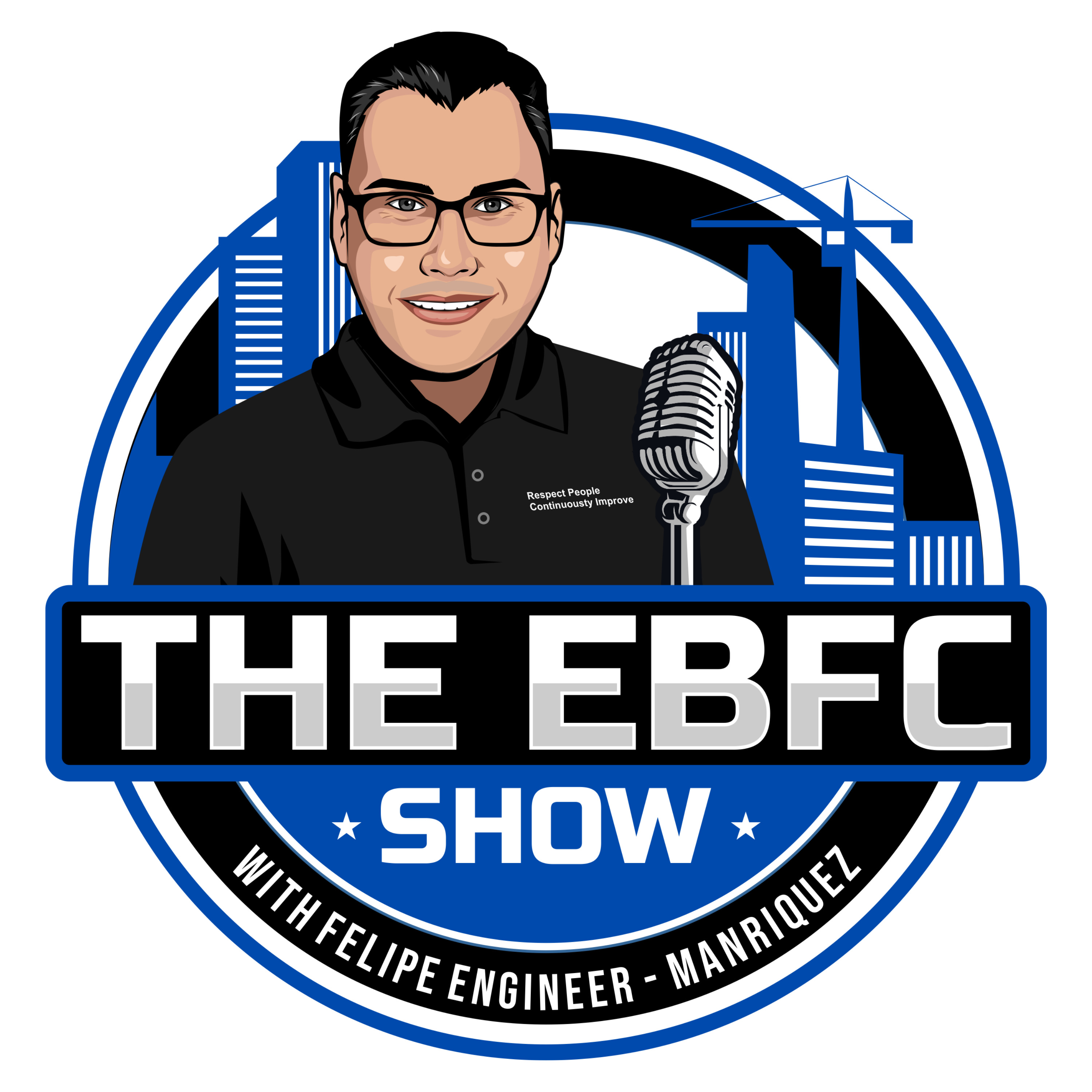
Hal Macomber says, “Lean is NOT a cost-cutting approach. Lean is a people development approach.” The current state of construction is changing. More and more people are changing how we build. In this continued interview, Hal shares what actions you can t...
Hal Macomber says, “Lean is NOT a cost-cutting approach. Lean is a people development approach.” The current state of construction is changing. More and more people are changing how we build. In this continued interview, Hal shares what actions you can take to build higher team performance while building new capabilities including his standard approach for improving project delivery. When we focus on people and improving construction flow, we will be engaged in better strategies to minimize the impact of variation and complexity.
"Use Flow as your improvement metric. Engage the people doing the work, that is how to make positive changes, and continue learning." Focus on flow, use Takt Planning, and heed the production laws. The Four Production Laws include:
- The Law of Variation
- The Theory of Constraints (bottlenecks)
- Little’s Law (batch size and durations)
- Kingman’s Forumla (capacity utilization and variation)
Free Takt Resources:
https://www.elevateconstructionist.com/taktbookresources
Free Construction Scrum Book Resources
https://constructionscrum.com/downloads
Connect with Hal via
LinkedIn at https://www.linkedin.com/in/halmacomber/
Connect with Felipe via
Social media at https://thefelipe.bio.link
Subscribe on YouTube to never miss new videos here: https://rb.gy/q5vaht
---
Today’s episode is sponsored by Bosch RefinemySite. It’s a cloud-based construction platform. Bosch uses Lean principles to enable your entire team, from owners to trade contractors – to plan, communicate, document, and execute in real-time. It’s the digital tool that supports the Last Planner System® process and puts it all together in one simple, collaborative ecosystem. Bosch RefinemySite empowers your team, builds trust, creates a culture of responsibility, and enhances communication. Learn more and Try for free at https://www.bosch-refinemysite.us/tryforfree
Today's episode is sponsored by the Lean Construction Institute (LCI). This non-profit organization operates as a catalyst to transform the industry through Lean project delivery using an operating system centered on a common language, fundamental principles, and basic practices. Learn more at https://www.leanconstruction.org
––––––––––––––––––––––––––––––
The EBFC Show Intro Music: California by MusicbyAden https://soundcloud.com/musicbyaden
Creative Commons — Attribution-ShareAlike 3.0 Unported — CC BY-SA 3.0
Free Download / Stream: https://bit.ly/al-california
Music promoted by Audio Library https://youtu.be/oZ3vUFdPAjI
––––––––––––––––––––––––––––––
Hal Macomber 0:00
It's crazy. And we get what we get late projects over budget, people getting injured and worse dying on our on the projects with good intentions. And it's ironic when someone dies in a building a hospital, it's like come on, and that unfortunately happens way too often. And we can make that go away. Just design productions, the production system to give a reliable result, a result that others are enjoying, whether it's in health care, they're enjoying it, whether it's in software, they're enjoying it throughout project production of, of goods and services. And thankfully, food all conforms to the sound production theory.
Felipe Engineer 0:46
And some of the systems thinking how that people may not be aware of happening inside of construction projects is there's this reinforcing feedback loop on individuals and project teams, you could have two teams in the same city, working for the same company, building different hospitals. And there's there are zero incentives for those different project teams to come together toward each other sites learn from each other. And I'm talking about the same company. So yes, there is there is zero incentive for those people to share and collaborate. In fact, as the companies are organized most typically, they're actually incentivized to not share and to keep things to themselves.
Sponsors 1:32
Welcome to The EBFC Show, the easier, better, for construction podcast. I'm your host Felipe Engineer Manriquez. This show is all about the business of construction. Today's episode is sponsored by Bosh RefineMySite is a cloud based construction collaboration platform that applies Lean principles to enable your entire team to plan, communicate and execute in real time. It's the digital tool that works in tandem with your last planner system process and puts it all together in one simple, collaborative ecosystem. This easy to use platform is available in English, German, Spanish, Portuguese, and French and can be used on desktops, tablet and mobile devices. According to Spencer Easton, scheduling manager at Oakland construction, refined my site in my opinion, is the best cleanest tool on the market for the last time. Here's what our users have to say. We've looked at three other digital scheduling platforms and none compared to the straightforward approach refund my site takes from milestone planning all the way down to daily tasks. This program gives every general contractor and their trade partners meaningful collaboration, accountability and KPIs. Registered today to try refine my site for free for 60 days. Today's show is also sponsored by the Lean construction Institute. LCI is working to lead the building industry and transforming its practices and culture. Its vision is to create a healthy and thriving industry that delivers outstanding project outcomes every time for everyone. Check the show notes for more information. Now, to the show.
Felipe Engineer 3:20
Incentivizing people to not share, keep quiet, not help each other that can be absolutely changed, you can influence that at your organization, there is nothing preventing you, especially if you're at the same company, from visiting other sites and learning what's going on. Especially if there's a gap and phase like if one projects a little bit ahead of you. You can learn immediately from current conditions there to help you predict the future on your job.
Hal Macomber 3:50
I mean, are you talking about two projects at the same kids go see things that are completely different? This practice of benchmarking in industry in general? You know, if you're if you're a specialty contractor doing, let's say transmission lines, yeah, you want to benchmark yourself against the people who are doing transmission lines, go benchmark yourself against somebody who's who's doing vertical construction. Like learn from the the I mean, calling a benchmark might be different, but I'd be wrong thing to say, but it's like, what have we never even considered because we don't think we have those problems. And that we go someplace else makes it mean a famous story about about oh, no visiting a Piggly Wiggly and, and seeing the way they stocked the shelves led to the development of the Kanban method. It's like replace only what you used. And it's it's like and then he visited a slaughterhouse for pigs. And the, the way they deconstruct ruk did the pig was the inspiration for flow? I mean, this is we would you and I would not be talking about Lean, which, in the background of all this, we talked about Lean design and construction, right? We wouldn't be in talking about it, because that would have never happened if Ono didn't get outside of the world that he was in. And he went to those two places. And by the way, he came to the US at the invitation of Ford. Right. So that magnanimous invitation that Ford made to Toyota, because the Japanese people really did need to get back on their feet. And then us couldn't supply all the trucks that were needed, so that they could do it. So the Japanese needed to be able to build the trucks so that they could get back on their feet. And Ford reached out and did that. And this is why it's not a grand Act of, of, of kindness. Just a small act of kindness, hey, Philippe, come see my my project, and maybe you could help me to win is like, see what I'm doing is like, maybe I could, it was something you could see that would make this go better. But we aren't doing that. Like, who would you Bill, your time to? Do you get to bill your time to your project, when you come visit me? When my project manager let you bill your time to my project when you come visit me? I mean, in some in some environment, that is not that would not happen. There. So rule, I'll say rule bound about that kind of thing. So let me just name the four production laws. I don't think we want to go into a lot of detail here. But the you can read about all four of these production laws in I think it's chapter three in the book. This is lane by mosaic and Ostrom. The one is the law of variation. And what we need to know is that variation compounds with dependence. And so the more variation you have, the more problems that you have. The second is the law of bottlenecks, or the theory of constraints. And that any change you make in a system, outside of the bottleneck in the system doesn't improve any of your doesn't improve your throughput. You need to know where that bottleneck is, and you need to be acting on that bottleneck if you want to improve throughput. The third one is littles law. And those law basically is a relationship between the batch size and the duration of work, whatever operations sequence of operations you're doing, the bigger the batch size, the longer it takes, the smaller the batch size, as soon as it gets done. You look at batches, the batch size that the you know, the industry kind of caught attention to this when in the remodel of the Pentagon. Hensel Phelps was the contractor. Actually, general probably I don't know if that's true general contractor probably was their role. But they had a five day takt a five day pace of working through a wedge and a floor of the building. And everybody had to do things in five days, that project was one of the most reliable projects that Hensel Phelps saw. And, and the industry and they were very, very happy to share what was going on and to the world fell and found out about but the difference between a five day takt time and and a 15 minute takt time. So on cruise ships, when they're remodeling staterooms, the tech times something like 15 minutes, a trade or an operation hands off to the next operation every 15 minutes until you start in the morning on a state room in maybe by maybe two and a half hours later. 10 operations later, that's turned over that's completely back in service. It's the refreshed in terms of carpet or ceilings or bedding beds or whatever they change over. Probably not 10 operations maybe maybe more than that. But if it's 20 That's only five hours. So every you know, it takes five hours to turn over the first one and every 15 minutes another one is ready. And imagine if the Pentagon had found a way to turn over slices in a much shorter period like every one day that project the renovation the Pentagon, Pentagon would have gone much faster.
Felipe Engineer 9:21
Now we got to visit a project hell when Jason and Spencer took me to Germany and on the western part of Germany there's a residential general contractor called Weisenberger bow that has moved from a five day takt to a four day takt and then recently, with a little bit of modularization of prefab gotten all the way to a one day takt with their partners. It's incredible how fast they're turning over spaces. I mean the speed at which those things complete and the quality is unbelievable.
Hal Macomber 9:56
So I've been doing one day takt from the beginning. And it's because I couldn't figure out how to do a half day takt. I got introduced to this by Doyle Wilson builders out of Austin, Texas they no longer around but this was back in 1997 or eight somewhere around there. They were building in Austin, they were building homes. Over 2000 square foot homes, four bedroom homes have configurable to the to the buyers desires in something like 53 workdays. So something like 106 distinct takt periods of a half a day. And I got it, we got to practice this at the Neenan company. That's where I was. And, and we did takt on a middle school addition to a parochial school. And we built a whole addition. And with a with labs, and I believe and indoor like a basketball court set or something like that cool what we got out of school like a week early, and they came at the end of this summer. And they came back two weeks late, something like that. And there was a middle school, and it was a one day tap. Oh, this is this is 23 or 24 years ago.
Felipe Engineer 11:28
Three months a whole new school. Yeah. Yeah. That's incredible.
Hal Macomber 11:37
Well, there was we did a lot of on site fabrication, not offsite prefabrication, on site fabrication of all kinds of things. So it's like, ERP before panelization. But Nathan was a, they did a lot of tilt up with architectural tilt up. And so they had a pretty good idea about how to do things off like not on the building, but then placed on the building. But in the in the work that I've done on this on troubled projects. Every troubled project is a kind of a two step process, stabilize a the process of making work ready. So that when you start something you can finish it, and second work to a one day takt and projects. I mean, the very first project in Boston was done with Suffolk construction for for the Massachusetts College of Art and Design MassArt who is a building that was two months behind because of ice storms during February. So this was in July, it was two months behind because of ice storms in February. And there was a hard turnover date for occupancy the following May. Can we finish two months early and without, without with very small incidental addition of people like overall, less labor on the total job. But we did a two day takt. I couldn't get him to do a one day tech. They they thought I was crazy enough. But they were so far behind the at least try to what I was doing. And that got stuck on a path that of doing takt on all their high rises. This is they don't even talk about it as tech This is just what we're doing. Yeah,
Felipe Engineer 13:36
I was working on a team. Speaking of the labor, I was working with a team in the Midwest. And when they adopted a tax schedule, they were like an 11 story cast in place concrete structure with like laboratories and you know, heavy duty stuff like heavy heavy concrete, big, big, big floor spaces, big floor to ceiling spaces. And they were having some issues with with concrete this was like during the the heart of the pandemic. So we had like the supply chain issues those they were facing, or the superintendent adopted takt I started realizing as he was onboarding new trades into the plan that what companies had assumed would be the labor that they needed to do this building was too much. All right, and I got to visit the site. After they had done two floors. They were on the second floor where they had already implemented the takt. They implemented the basement first on the first floor and so on. And on the first floor they were halfway through the first floor before they were going to move up to the next level with all the MEP and framing crews and the sheetmetal Foreman said okay, I believe you now it's been long enough. I have too many people. I'm going to send some people and I'm just going to keep you know these many people instead. And everybody was like yep, yep all the others. grades were like, yep, yep. Like it happened to all of them at different points and, and he was the last holdout, you can get much more reliability. So like imagine you're on a construction project and you can keep the same people the entire time. You don't have this up and down in trade, trades people up, and then laying people off and then bringing them back or sending them away. Or you can keep a steady crew the whole time when you use takt. I can't look good things about that.
Hal Macomber 15:28
Yeah, a takt construction is what we need to adopt. And it's the only approach we currently have. That conforms to all four production laws. Let me speak about the fourth production law. Kingmans called Kingman's Formula, or it's generally the way people talk about it. It's a relationship between your capital your capacity utilization, and the presence of variation. So a simple way. And so what it means is that as, as utilization goes up, and variation goes up, you get a curve that looks like this. And that curve is called the delay curve. Like how much delay will you incur? Well, no utilization, like empty highways, at two a m, you're getting almost no variation from other drivers, you've got wide open spaces, you're gonna have no delay. But as the as you have more cars, you have more variation, as you have more utilization, these compound, and it took three hours to go in Boston, two to three hours to go 20 miles.
Felipe Engineer 16:43
Right? Perfect, you get traffic jams people.
Hal Macomber 16:47
And we have the same thing on job sites, the fundamental, the fundamental reason our projects are late, is we drive up our utilization of our resources. And we don't address the variation that we're incurring. So we have high variation, we have full utilization for promised work for work, that's no kidding, that needs to get done. And then we have a delay. And that delay just keeps compounding. And so you get the curve that goes like that.
Felipe Engineer 17:17
Right and the knee jerk reaction for people that are running work, the stereotypical or what people are trained not even started typical. This is just what is tradition is that when something on the critical path falls behind, everyone wants to add more bodies to it. And adding more bodies to add more people to it is going to ignite kingman's formula, and you're going to see more delay. And I've never seen an example in 20 plus years, where some critical activity was late. More people are added for two weeks, one week, three weeks a month, it doesn't matter. It never recovers. I've never seen a recovery. And what I have seen when recoveries happen is that people work on flow and throughput. Right? We need to talk about flow you promised me well talk about flow.
Hal Macomber 18:05
So that's the next topic. So let's put the period here at the end of these the design this system from for according to the laws, the next thing is use flow as your improvement measure. So it's not like it's not the point of the system, the point of this system is to deliver what's promised. But how do we do better and better at delivering what's promised takt construction a takt construction approach is a flow approach, but you're not going to get it right. And there's going to be enough variation in the nature of the work that you have to adjust along the way, or you break flow. So we use flow as an improvement measure to tell us by like, when we we thought we thought we had the work was ready for the people, the people and the resources, were ready for the work. So the tooling and the materials, right, as well as the people and and we had all the permissions we needed from whatever Jersey jurisdiction jurisdiction having authority or whenever it was needed. Penyet it stopped. Why did it stop? It's that moment that we that flow stops that we need to capture. It's like, not just fix it, not just say okay, hey, we need to find someplace for these four people to work right now. And you send them away. No, no, no, don't just do something stand there. You know, it's the opposite expression. Don't just stand there. Do something. No. When flow, a break and flow happens. Don't just do something stand there and capture it. Why did it not flow? It's only in that moment that we can take kind of understand. What might like that's that's like that's the The outcome of the something was not understood that it stopped. Why did it get that way? A good five, why might take you back to figure out why it might not. But capture, take a picture, make a note in your daily report so that we're very clear, then address the situation and get people find someplace for work if that's what's needed. rectify the situation and get them back to work there. If that's if that's available, but you want to investigate the breakages and flow and constantly work on that we do not have I do not know of one company that is paying attention to flow. And I'd love to hear from the 1000s of listeners that yeah, we're one of them that are you doing exactly what you're saying how. But at a company level, to my knowledge that there isn't one that is fixed on that. So far, Martin sin I've heard has adopted tech and is adopting tech construction company wide. And they're going to have to deal with this or they're going to be failing. I know, they were well trained. from P2SL from Iris Tommelein, and some of her colleagues. And they got their training quite a while ago, I was just talking to Iris two weeks ago about this. And, but they've committed to it, they're all in now. And so they're going to work this out, they're also going to work out how to manage buffers in their environment, a buffer capacity buffer because you can't work to full utilization. And so you need to swing capacity of labor, you need to build a plan, yes, like, Okay, if they're not needed here, they're over here. And then we can swing them in without disrupting the flow of work for other people. We need additional work in process inventory for people to go to if they if they're on a track takt wagon, and for whatever reasons, they're getting into, let's say it's apartments. And there's three studios in a row that each have one, one bathroom, as opposed to the usual one and a half, well, you don't need all the plumbers, if it's gone down to just that small amount of work. So swing them off of that work on to workable backlog. And then the third one is time buffers. And everybody's used to time buffers, we call it float, we design an in on projects. But that doesn't help the client to put all that extra time in. So it's managing a number one identifying where your buffers are needed, and then managing those buffers so that you don't brake flow. And all that needs to get figured out. That's the lease that piece of tech instruction is the least understood.
Felipe Engineer 22:52
The training with Jason Schroeder that with the work done by Marco Binninger and Janosch Dlouhy. They've done some incredible work around understanding what they call tap control, and subtle tap control. And all those things that Hal just mentioned, there are strategies for setting those buffers and using some parameters, to understand that those are set appropriately so that when flow is interrupted, it doesn't disrupt the throughput or the overall time there's no impact to the client. And there are I mean, people there are definitely strategies out there. So if you want to learn more, we'll put a link in the show notes for Jason Schroeder's page where he has all the papers from Yash, and Marco, and Iris as well, that you can read about more of these things. Or you can just take the training with Jason, and learn how to implement this, yourself, I highly recommend I've taken it myself. It's very scrum friendly. And I it's it's a good time.
Hal Macomber 23:52
So first thing that we have to do change the design of production sites. The second thing we have to do is improve on the design by using the flow as as your improvement metric. Third thing we have to do is get all the people with their hands on the tools and material involved in improving their work, and thus system. And of course of doing both of those things, a carpenter that's improving his or her work, and as a consequence of system, develops critical thinking skills, creative thinking skills, and learns how to make change that sticks. Like what could be better than to have the army not just the second lieutenants and above, but have the army improving on what they're doing, and how they're doing it, and learning as a result of it. And that by the way, the Japanese call Kaizen improving people through improving the work and and the product.
Felipe Engineer 24:55
This is what we see typical in the Special Forces and military. I've been to Have roll agile conferences, and heard presentations from people in different militaries not just in the United States, but also abroad. And this whole idea of bringing agile, and it's been very widely adopted in Special Forces, like here in the United States, the Navy, the Navy, the Marines, two branches that I know of that have adopted this, to some degree, also the Air Force. But like how you're completely right, like, think of how different it is to have everybody on the team, let's go back into construction, forget the military for a second. But it can be your project team, which includes the all those different trades, and the people leading the work that are responsible, like those general contractors, or some of the other people involved in production controls, or what they call project controls, or you know, cost and schedule. And having people involved that are actually at the front doing the work, giving them the opportunity to be involved, I would say it's not so much developing their capacities, it's as much as just allowing it to occur. Because in the in the current system, it's not encouraged or really allowed, and phrases to prove to you that it's not allowed. If you've ever been on a job, and you've heard this phrase, keep your head down, and just do your job. Or just do your job or cease zero process for getting feedback on how the work is going. Or there's never any pause to reflect if a week's worth of work occurred. And in the course of all the meetings that that team has, there is no solicitation of feedback or looking to see the progress and making adjustments. There are no feedback loops, and you're just marching off a cliff. And so those are all that's all evidence people that you have opportunity to do some of the things that Howell is talking about, and make the small changes and these changes are they're tiny, they're teeny, tiny. And they have massive impact. Like we're talking about tax. It's very common on a tax schedule. In Europe, and from the people I mentioned, the papers written, I've heard of over I think we're now over 200 different case studies back to back to back jobs using tax where schedules have been improved, as much as 60% 70% in some cases. So the vast typical, is twice as fast if you just think about that. Whatever job you're on now. It can finish two times faster. With stable crew sizes. And buffers.
Hal Macomber 27:49
And buffers, right? Yeah, right. And buffers. Yeah. And Felipe is not exaggerating at all here, I get routinely 30% Faster projects. Without aggressive takt, like one day takt, like two day tech two day takt will be 30% Faster than a typical schedule. And
Felipe Engineer 28:14
then I've done some schedules, I mean, just to show that this works even in support areas on just designing cordoned coordination, where we're looking at clashes as we bring elements in and complete the design on either design build or traditional design bid build. Or we're coordinating the final details that were not designed using light takt. I've seen multiple times on multiple and multiple geographies, in the south of the United States and the West of the United States and the east of the United States. Different projects have different project types, all saving more than 50% of the time. So it's twice as fast coordination. And we're actually giving the detailers and the people running the CAD more time to do the work and not less right you have the more time to do the work. And because of how we sequence the work and takt it sounds like magic people until you go up. But how knows because he's done it to any detail schedule. If you're out there and you're struggling and you want information, contact myself for how we can talk to you about how to implement this. So you can cut that design schedule or that coordination schedule in half. And you're still giving the detailers more time. It's incredible and it's very stable. Your quality is gonna go up your clashes are going to go from 1000s to a handful.
Hal Macomber 29:33
I think there's a good moment to say that we've misunderstood lean, like an industry as a cost cutting approach.
Felipe Engineer 29:45
Yes, it's a people. That's worth saying twice now. We've missed some of Lean industry wide people just do it with just cutting cost, right. Incorrect.
Hal Macomber 29:57
Yeah, it is a P Bull development approach. That's what it is. So it's, it's a human resource strategy that masquerades as an operation strategy. And until we get it, right, that it's a human resource development strategy, that we're changing the relationship that people have with their work. And with each other, it's essential that we change the relationship they have with the work, that they're improving the work for the benefit of themselves and others. And in the course of doing that, they get smarter, they get more competent, they get creative, they learn how to get shit done. I mean, this is, this is what the Japanese have been doing for a long, long time.
Felipe Engineer 30:46
Evidence of that we see people, Americans and Japanese alike, that work an entire career at companies like Toyota, and there are others. But I'm just going to name my favorite so happened to drive a Toyota car myself. But when those people leave the company after their career, voluntarily, because, again, the company has lost on percent attrition, I mean, as virtually nobody quits, when you have your attrition rate is less than 1%. That's nobody quitting. Okay, so just think about that, as you look around, and average construction attrition rates over 25%, typically, across the industry, for companies large and small. That means one out of four people are moving in and out, either voluntarily or involuntarily, every single year. So at Toyota less than 1%. And then you've got those individuals, when they retire, they don't retire, they come out and they start writing books, they start consulting, they start working in other industries to helping their level of creativity is so high, that they just can't sit still. They're on fire with their ability to improve things, and they're out there across industries, helping so many people.
Hal Macomber 32:00
Yeah, and you're making a really interesting point, they've learned so much, that they can go into an industry that they've never seen before. And they immediately can see how to help people, they're not to do things for them, help people there take better care of themselves. And that that switch, kind of like the Six Sigma thing about parachuting in some, no master black belt to solve the problems that you've got on a production line, it's all bullshit. And it's incongruent with Lean, no, we want to come in. And the first thing we want to do is stabilize the environment, and then help people take better care of themselves and each other. And as soon as they catch on to that they're taking better care of the client, than they're taking care of better care of the company. And it's in that order that that you need to do it, take care of yourself, take care of each other, take care of the client and take care of the company. And it's at essence of what this is all about. And when I say that, there, I'm sure there's listeners who are saying, Yeah, but we're not all one company. Right? So let's get to this next, this next thing, and it's called trust. So I said at the close of our the first part of this, yeah, if Fernando said the basic, the reason why we're stuck with the system that we have, is we operate from a position of distrust. And that's codified in our contracts, it's in the basic ways that we do things owners have, you know, this, the schedules are baseline so that the owner can, can make claims against the contractor and vice versa. Like we're counting on everybody screwing up. And it's, and they need to be blamed for it, as opposed to we need to work together so that we can take care of the people and a client that they distrust is going to keep us from making the change. And Fernando at the very close to the end of his keynote, where the international group for Lean construction in 2021. He said it's that we don't have affection for each other. That maintains the distrust. We need to have affection for each other and until we purposefully work on that. We're stuck with it. Now having said that IPD integrated project delivery projects. There is a lot of work that is done on enhancing improving the relatedness as I said in the five big ideas that we've got to change the relatedness of one to the other and we're talking the plumbing the the electrician and the mechanic is like, at every level in our projects, not just among management with the owner and design teams, etc. No, no, no, every level. And at least until we increase the relatedness. And now that's the way I said it, whatever, 18 years ago, kind of clumsily, but I picked that way on purpose. So people would have to say, What the heck is he talking about? I love that Fernando said no, no, no, we don't have affection for each other. This is until we do that we are going to deal with the distrust issue. And he said that to civil engineers with PhDs, kind of like, Ah, okay. Pretty funny. But this is I, I can't disagree with him. i He went further than I did. 18 years ago, I've, and I'm like, Yeah, but along the way, I learned about the outward mindset, you know, treat people as people not as, as objects, who could help you get what you need, or being in the way of what you're pursuing, or just irrelevant. No, treat people as people who are like you, they have concerns and take care of them while you take care of yourself. I'll say for everybody listening, leadership, and self deception is how I got introduced to this idea of the outward mindset. It's by the arbiter Institute. And they, there's a couple other books, the they have a book that's titled titled, The outward mindset. I've read, I've read those books and and others that they've written, I still would say, start with leadership and self deception. It really helped See, for me to see where I have the inward mindset, and how often I have an inward mindset. Not like because I want, I choose to be inward, and some people are just inward, it's like, if I don't look out for myself, nobody else will. And I got proof that each time I let my guard down, I get screwed. Alright, so I definitely want to look out for myself because nobody else will. As opposed to just be generous. Just be loving, have affection for each other, take care of each other, and take care of yourself. Which means ask for help. If you can't do it, if whatever you need to do, you can't do yourself. And you and I are in a community of of Lean practitioners where this goes on constantly. And the few people in the community of Lean practitioners and lean leaders that have an inward mindset. It's like we don't it doesn't stop us from continuing to engage with them. Right? Anyway. Well, we're helping them anyway. Yeah, yes, like, they're stuck, whatever, they're stuck, it doesn't matter. We can help them and we can we can move on. But this approach of, of, of really seeing each other as humans respecting their humanity, with, with the faults that we have with the errors that we make, usually, neither our faults or errors are with intent. You know, there's criminals in the world. Yeah, it's a small percent. You look at our police forces, and you wonder, like, we must be a huge percent, but it's, no, it's a small percent. So we can be, you know, we can be prudent. At the same time, we take care of each other and take care of ourselves.
Felipe Engineer 38:42
I've actually been criticized by people in the industry for being too generous, and helping people and acting in a way where I'm never asking for work. And I build this time to write that type. And I have asked those people that have given me the criticism, like right there. And then I said, what's the alternative? If you see somebody in need, and you just walk on by and don't help them? What is what does that do to you that has a consequence on you as well. And I learned early on. Luckily, people helped me when I needed help, even though wasn't at the time able to vocalize it. And I received some help. It made a massive difference in the quality of my life and the quality of my work. And from that moment forward, and that was over a decade ago. I just erred on the side of being generous, like you said, Be generous when you can and just help people. And I always tell people in my shows, like if I if you ask me a question and I can't answer it, I probably know at least somebody else that can and I'll get you connected to the person that can because you don't need to struggle by yourself. We are a collective. We're going to be with the work that Hal and I are talking about. We're going to be more affectionate with each other. And we're going to help more people, we have the capacity to help more with our experiences, we want to help more, all you have to do is ask, reach out. And we will.
Hal Macomber 40:14
We must do this work the planet. So it's my grandkids, kids are depending on you and I and everyone else here to do this work.
Felipe Engineer 40:28
That reminds me of the company, Seventh Generation Hal, where they said, the Native Americans are the indigenous people. They have this concept of making decisions and thinking seven generations from today. And so that's a powerful like you said, I mean, just in your conversation, just to think three generations be past ourselves, right is a massive improvement, or thinking about the stresses of every day where people are trying to make decisions on, you know, what's going on this month, this week. It's very short sighted, and you could be on a path. Like Cynthia said, The world is on fire, and you can't you don't even notice it, because you're just thinking about the next five days. I mean, you just look out the window and see things burning. Right? Where I live in California, how that literally happens, like we look out the window, we smoke an entire entire cities disappearing, and fires because we haven't maintained our forests. And the third way, go have government fighting with government agencies find with other government agencies, you know, is this federal land is a state land, you know, where's the source of this fire? Instead of thinking like, No, this is land where people live, let's figure it out and cooperate to our mutual benefit to win win to be affectionate with each other, regardless of whose budget is it coming out of? Because if we don't do something, people are going to die.
Hal Macomber 41:55
And that sounds crazy to be affectionate, without, without regard to whose budget? I mean, it's, we're in a bubble. We're in a bubble, we the bubble is the industrialized, the age of industrialization, right? And with the cost accounting practices with the mass production practices, it's unavoidable. And like, why would we think about? Well, yeah, when it goes, spend time with that team? Who am I charging it to? Like this is, we're gonna be such more so much more powerful. But if you only get paid by the hours, you bill, and engineers principally get paid that way the firms get paid that way for the hours that they bill. How do they get motivated to get rid of the failure demand? How do they get motivated to find more innovative ways of delivering, it's just less hours that they're going to build, they certainly if they're working for government agencies, they can increase their rates because the multipliers are fixed. And you got to begin looking at it. That system is perfectly designed to produce this broken result that we have. No, perfectly designed.
Felipe Engineer 43:09
I've heard people get on the social app clubhouse, where people can talk to each other. And I've heard contractors say this, I know how to make money and extract from this broken system. I don't want it to change. I've heard that more than on one occasion. And I just look at those people. And I just think, yeah, but you could make so much more money if you don't extract and instead, enhance. If you enhance the environment, and go for a win win. You can actually make phenomenally more money. Back When Hal and I are talking about completing these projects, just using some of these things like takt with subtle control, tap control, over war, taking months off of a job, guess what happens to your margin your profits, it exponentially goes up. And you don't have to, like use heroics, and suffer on the job to get it done. You don't have to sacrifice time with your families. To get the job belt. You can do it like a professional. And you can plan and have a very reliable schedule. I've been with superintendents how that are using takt and Scrum on their projects. And an eight hours of walking with them and being with them. Their cell phones ringing one or two times. That's it.
Hal Macomber 44:34
Yeah, that's not the usual experience of an area superintendent. Right. Right. Yeah.
Felipe Engineer 44:41
So that's, that's what we're offering. You know, this different type of thinking and the tools are available to you there in the in the public domain Alec House talking about things that have been in practice for 30 years. We just have to get we're getting the word out there. People are getting the word out there so you can get access to the stuff. If you've never heard of it? Well, you've heard of it now. So this is at least the second time you've heard to say takt. And this is the millionth time you heard me say Scrum. So don't act like it's not available to you. These these things are out there. And you can learn about them for free. Now, you've got to create, like when Howell said, he goes to projects, I love that you said, Well, there's two things you do when you go to a project that's in trouble. First thing you do is you stabilize. Right? Is that what you said? That's right,
Hal Macomber 45:27
I said, and in particular, focusing on making work ready. That's right when so that as early as we can, people are now starting work that they can finish. And they immediately see that that's different from what they've been doing. Because you see piles of inventory and go back spaces and all that stuff on most jobs that are in trouble. So you stabilize with by making work ready. And then the second thing is, you work on tag construction
Felipe Engineer 45:59
period. Because we're you're working on because that gets you into a whole systemic approach on a permanent flow, right? Low rates, workflow, logistical flow and trade flow. It's incredible to do those things. And I have the same approach. When I go to jobs that are in trouble. The first thing I do is I want to improve the capacity for each person if we're because most jobs that are in trouble, you have people operating near 100% capacity, which is unsustainable.
Hal Macomber 46:26
Oh, they're over there over 100% or over 100. Right. So someone is starting to recently 27 days in a row of 12 hour days. Right? How do you do it? That's means you're working every weekend, right? 27 days in a row.
Felipe Engineer 46:42
And the stories of how many jobs are working weekends are too many to to recount, right. I remember going to a presentation and there was a project director was like bragging that they had a Saturday and Sunday rotation schedule. And I saw executives in this presentation like nodding their heads like yep, that's how it's done. Like, no, that's not how it's done.
Hal Macomber 47:07
That's a sign of failure. And then exactly if it's you've designed in failure.
Felipe Engineer 47:09
And upon further investigation, that project had a punch list in the not 1000s of items in the 10s of 1000s of items. And so there's a high cost of rework that's not tracked. And you mentioned accounting principles, and the current accounting principles, how we look at things, the way that we track completeness and doneness, people just jump over the fact that go backward costs you money. The general contractor cost them to manage and coordinate people coming in and out of now occupied building, if it's vertical construction, and then all the trade contractors, they're all charging, and they've built that in to the contract. They've built it into their price, but it's eroding their margin, because it's not finished.
Hal Macomber 47:58
Well. And not only that, but their profit velocity, the rate at which they earn their profits goes, Just goes to hell. Wary as you take a flow oriented approach, using tap construction and and conforming to the for production laws, you your projects are shorter. So the time period that you're going to earn your project is seven months as opposed to 10 months. And your fixed costs are lower, you get all those porta potties you're not renting and the Wi Fi that you're not paying for and all those fixed costs go away. So your profit goes up, the duration goes down, and you easily see a 40 easily see a 40% increase in profit per month for the job. If you get longer time, you've got more, you if you go beyond your your due date, a 12 month project versus 10 You get that extra to 20% more fixed costs you make that means you're making less money on his on his on his stipulate some project over a longer period, the profit velocity is so small, it could be less than half of what you're you were intending to make. And because you're longer you've got more risk or likelihood that people are going to injured if you've if you've escalated, you got more people on the job. That means one of the worst times escalation on a project is the worst time for any project because you know you would have more injuries period not just because you got more numbers but because of the interaction of all these people who don't know each other don't know the work don't know the site. It's it's just terrible.
Felipe Engineer 49:41
Now thank you so much for coming on the show. I can't believe how fast the time is scooted by us in this part two, you get the last words.
Hal Macomber 49:50
Let's just start with this respect for people thing we've got to break this this wall of distrust that is keeping us from making the kinds of improvements. So get to know people get to know people that are around you every day and in a way that you are generous with the care that you're providing them, that you bring love to the situation that you're in.
Felipe Engineer 50:18
Very special thanks to my guest. I'm Felipe Engineer Manriquez. The EBFC Show is created by Felipe and produced by passion to build easier and better. Thanks for listening. Stay safe everybody. Let's go build!